HOT BRIQUETTED IRON-C-FLEX PROJECT: Addressing a Challenge to the HBI Value Chain
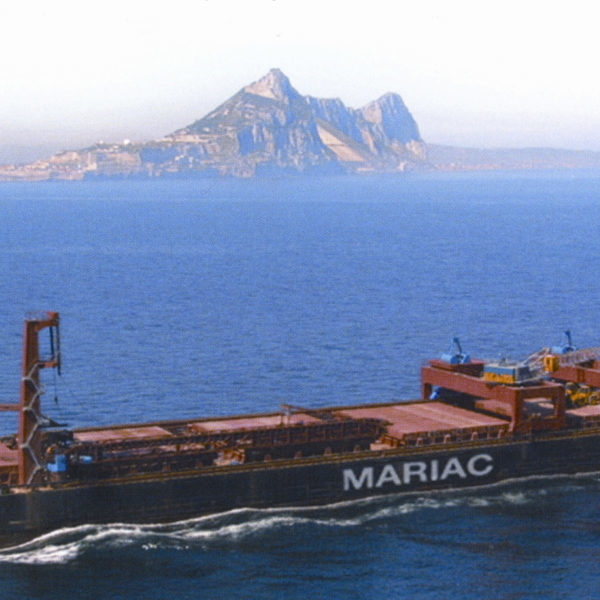
INTRODUCTION
Hot Briquetted Iron (HBI) continues to grow in importance as a merchant feedstock for the global steel industry, with a significant volume of trade involving maritime transport. The pace of growth can be expected to accelerate as the steel industry progresses along the pathway towards decarbonization of production.
Maritime transport of HBI is governed by the regulations of the International Maritime Organisation (IMO), which include specific provisions for all forms of Direct Reduced Iron (DRI). Therefore, it is essential that changes in the characteristics of HBI are properly reflected in maritime regulations.
Several emerging trends have the potential to challenge the status quo with respect to safe shipment of HBI, notably decarbonization of steelmaking and the expected medium-to-long term shift to hydrogen-based HBI, and in the shorter term, the trend towards flexible and higher carbon content of HBI. IIMA has started a project called HBI-C-Flex to evaluate the impact of these trends on reactivity of HBI and safe shipment.
THE GENESIS OF HOT BRIQUETTED IRON-C-FLEX
This story has its beginnings in the 1970s, when HBI started its journey to becoming an established part of the global steelmaking raw materials supply chain – indeed this author travelled to Venezuela in 1975 to procure a trial cargo of FIOR briquettes for the EAF steelmaking industry in the UK. As is well-known, HBI was developed as a densified form of DRI in order to overcome the risk of self-heating inherent with shipping DRI. Over the years, the Venezuelan HBI producers, working together with IIMA’s predecessor organization the Hot Briquetted Iron Association (HBIA), developed a generic specification for HBI that was aimed at safe maritime transport. A key element of this specification was density >5,000 kg/ m3, accepted after much debate by IMO in 2008 for inclusion in the International Maritime Solid Bulk Cargoes Code (IMSBC Code) that came into legal effect in 2011.
HBI has the bulk cargo shipping name “DIRECT REDUCED IRON (A) briquettes, hot moulded” in the IMSBC Code with the following description:
Direct reduced iron (DRI) (A) is a metallic grey material, moulded in a briquette form, emanating from a densification process whereby the DRI feed material is moulded at a temperature greater than 650°C and has a density greater than 5,000 kg/m3. Fines and small particles (under 6.35 mm) shall not exceed 5% by weight.
Fast-forwarding several years, IIMA’s Technical Committee noted the developing interest in DRI/HBI with variable carbon content, ranging from the traditional level of 0.5-1.6% up to as much as 4.5%. A consequence of HBI with higher carbon content is lower density, which in turn raises the question of safe maritime transport and the IMSBC Code; i.e., at what density does the reactivity of HBI increase to the point that it behaves more like DRI with its attendant risk of self-heating thus requiring more comprehensive safety precautions, notably the need for ships’ holds carrying DRI to be inerted with a blanket of nitrogen?
Information and scientific data behind the selection of a density of >5,000 kg/m3 for safe shipment have proven difficult to find. Much of the research on this topic was conducted in the pre-digital era and it appears that many of the relevant files have been lost or destroyed for one reason or another. Therefore, we decided to conduct a literature search as the first step. The Austrian metallurgical research organisation K-1 MET, together with the Ferrous Metallurgy Department of Leoben University, was commissioned to carry out the project, which was designated HBI-C-Flex.
BROADENING THE SCOPE
Fast-forwarding again to the present, one of the over-arching preoccupations of the global steel industry is the goal of an 80- 95% reduction of CO2 emissions in steel production relative to 1990 by the middle of the 21st century. A key component of this vision of carbon-neutral steelmaking is a progressive, but not necessarily total shift from the integrated Blast Furnace/ Basic Oxygen Furnace (BF/BOF) to the Direct Reduction/Electric Arc Furnace (DR/EAF) steelmaking route, with hydrogen- based DRI and natural gas-based DRI with CCUS (carbon capture, utilization, and storage) progressively replacing conventional DRI.
Figures 1 and 2 are based on data for the Sustainable Development Scenario from the steel chapter of the International Energy Agency’s “Energy Technology Perspectives 2020 report (1). The total DRI production of 411 Mt predicted for 2050, when compared with the 108 mt produced in 2019, represents an increase of 280%. This article will not debate the likelihood that such a scenario will eventuate, but two aspects are relevant from the perspective of HBI-C-Flex. Firstly, the question of where will all this DRI be produced: integrated with steel plants, integrated with iron ore operations, or somewhere in between? The answer is probably all of the above. But whatever the case, it seems highly likely that a significant proportion of DRI will be produced in the form of HBI and transported internationally by sea. Furthermore, an increasing proportion of this HBI will be hydrogen-based and contain little or no carbon. What are the implications of this for safe shipping?
Secondly, this greatly increased DRI production will have profound implications for iron ore supply. The market for DR-grade pellets (and pellet feed) is currently very tight and IIMA’s analysis suggests that the current and planned supply of DR-grade pellets will be fully utilized by around 2030. This means additional supply will be needed and/or the direct reduction industry will have to utilize a proportion of lower grade feedstock. In the latter case, the issue of HBI density and safety of shipping again arises.
Thus the scope of the HBI-C-Flex Project has become multi-tracked:
- HBI with little or no carbon (H2– based)
- HBI produced from lower grade iron ore
- HBI with high carbon content
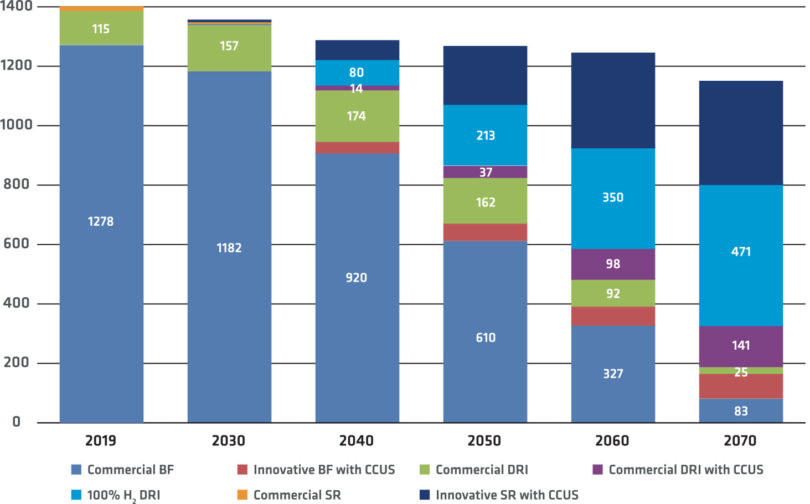
FIGURE 1.
Iron Production by Technology in the Sustainable Development Scenario (mt) (2)
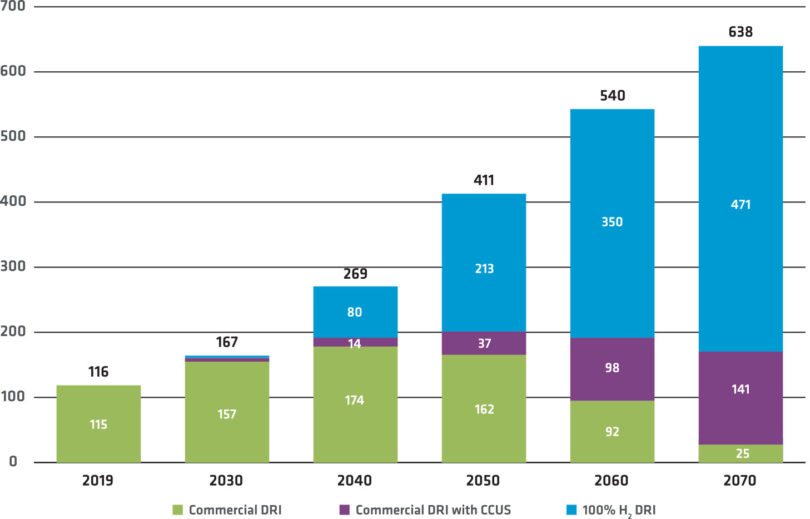
FIGURE 2.
DRI Production by Technology in the Sustainable Development Scenario (mt)
RESULTS OF THE LITERATURE SEARCH
Whilst the search revealed a reasonable number of scientific papers and articles, none of them provided the basis for the >5,000 kg/m3 density threshold. The impact of the chemical composition and mineralogy of the source iron ore, as well as the reduction conditions were barely investigated and discussed. Nor was there a clear interpretation of the effects of the carbon content. Importantly, considering the interaction between the various parameters influencing DRI reactivity, assessing each of them in isolation is not practicable. A reasonable interpretation might be that the choice of >5,000 kg/m3 was a case of “applied science” with a practical outcome.
Therefore, we concluded that a systematic study is required to investigate the various parameters considered as being the principal drivers of reactivity and thus the self-heating hazard. The study should seek to establish a correlation between these parameters and DRI/HBI reactivity and thereby fill the knowledge gap in the literature. A laboratory-scale concept has been developed to study DRI/ HBI reoxidation behaviour, taking into consideration the principal HBI production process steps from direct reduction of the iron ore to hot briquetting of the final product.
Ultimately, we hope to develop (1) a standardized approach to measuring DRI reactivity, (2) a predictive model relating the self-heating tendency with cargo properties, and (3) a process and guidance for risk assessment and control to underpin the paramount goal of safe handling and transport of HBI at sea and on land.
At IMO, the various types of DRI have a higher-than-average profile due to incidents in the past, meaning that to arrive at a basis for either a new schedule for lower density HBI or an amendment to the existing DRI (A) schedule, a well argued, scientifically based, and peer reviewed case will have to be presented.
It should be noted that the IMO process for addition of hazardous cargoes to the IMSBC Code can be very lengthy, thus necessitating careful and thorough preparation with safe shipment being at the top of the agenda.
THE NEXT STEP
HBI-C-Flex is a project that has important implications for industry participants along the HBI value chain in its broadest sense. The study as outlined above would be a multi-year project and given the accelerating pace of movement along the pathway to carbon-neutral steelmaking, IIMA intends to engage with potential project sponsors over the coming weeks to secure support to commence this vital research.
For further information or to discuss participating in the HBI-C-Flex Project, please contact Chris Barrington, Chief Advisor, International Iron Metallics Association (IIMA), at: cbarrington@metallics.org.
Reference Notes:
- Data kindly provided by IEA
- The Sustainable Development Scenario (SDS) sets out the major changes that would be required to reach the main energy-related goals of the United Nations Sustainable Development Agenda, including an early peak and subsequent rapid reduction in emissions, in line with the Paris Agreement, universal access to modern energy by 2030 and a dramatic reduction in energy-related air pollution. The trajectory for emissions in the Sustainable Development Scenario is consistent with reaching global “net-zero” CO2 emissions for the energy system as a whole by around 2070.