Hot Briquetted Iron: The Multi-Purpose Metallic
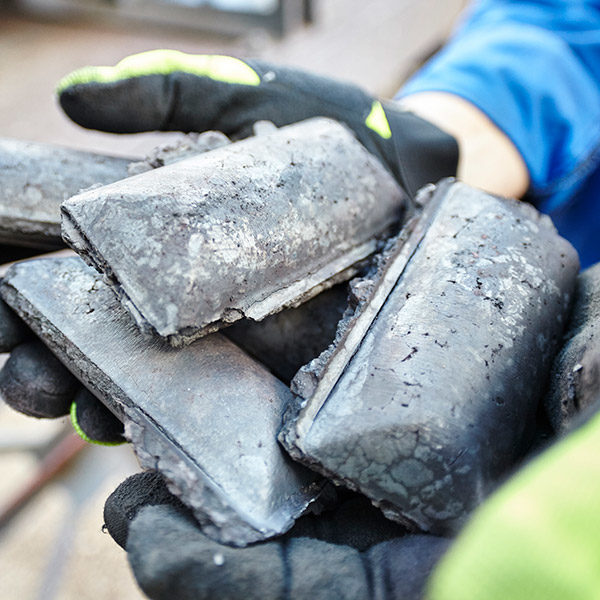
Here we are today touting natural gas-based Hot Briquetted Iron (HBI) as the immediate, transitional solution to CO2 emissions by blast furnaces (see the article in this issue titled, “HBI: Steel’s Most Versatile Metallic In the Transition to the Hydrogen Economy”). If we look back almost 40 years to 4Q1982, Midrex was introducing HBI as “A New Product For Big Steel” and promoting its value for thermal balancing and trim cooling in the Basic Oxygen Furnace (BOF).
Through the years, Direct Reduced Iron (DRI) has been identified primarily as a low residual charge material for the Electric Arc Furnace (EAF). However, the increased density of HBI has extended the productivity and environmental benefits of DRI to the Blast Furnace (BF).
HBI is recognized as the preferred form of DRI for ocean transport by the International Maritime Organization (IMO) in its International Maritime Solid Bulk Cargoes (IMSBC) Code. As such, it is shipped from plants located in Russia, MENA Region, Venezuela, USA, and Malaysia, to steel producers throughout the world.
Initially, the use of HBI in the BF was seen as a way to enrich the metallic charge to the BF, as productivity was the driving factor of the time. Two integrated steel mills in the USA used approximately 385,000 tons of HBI in 1993 and increased their usage to close to 500,000 in 1994. One of the mills, AK Steel, reported a productivity increase of more than 22% by operating with HBI as part of the BF metallic charge.
Today, the focus has shifted to reducing CO2 emissions from BF operations. HBI, which is metallized beyond 90% only needs to be melted; therefore, HBI use in the BF decreases the consumption of reducing agents. It has been demonstrated that a 10% increase in the metallization of the BF burden results in a 7% decrease in the coke rate, which in turn reduces CO2 emissions. If 100kg HBI/t HM is used, the reducing agent rate (coke equivalent) can be decreased by approx. 25kg/t HM.
However, the productivity boost from adding HBI to the BF charge is still a highly sought-after benefit. voestalpine Stahl, has found that productivity can be increased up to 10% per 100kg HBI/t HM by using HBI from its MIDREX Plant near Corpus Christi, Texas, in its BFs in Linz, Austria (see the article by voestalpine Stahl in 3Q2020 DFM for further details).
I was fortunate enough to be involved in the start-up and operation of the first MIDREX® HBI Plant on Labuan Island, Sabah FT, Malaysia, that was owned by Sabah Gas Industries. The plant made its first commercial shipment of HBI in 1984. In 2020, the plant, now known as Antara Steel Mills (HBI Labuan), operated over its annual rated capacity (650,000 tons/year) and came within 6% of setting an annual production record. Total iron of its HBI was the highest of all MIDREX Plants, averaging 93.04% for the year. All production was shipped by water to third parties.
So, here’s to you HBI – the steel industry’s most versatile ore-based metallic (OBM). Whether you operate an EAF or a BF/BOF, there is a benefit waiting for you in the use of HBI. It also can be used in Ladle Metallurgy and foundry induction furnaces. The International Iron Metallics Association (IIMA) is studying what they call Hot Briquetted Iron-C-Flex (see the article by Chris Barrington in this issue) and Midrex is evaluating various forms of HBI.
HBI is truly the multi-purpose metallic, and it will play an ever increasing role as we transition to the Hydrogen Economy.