Diluent Effect of DRI – Steelmaking Superpower
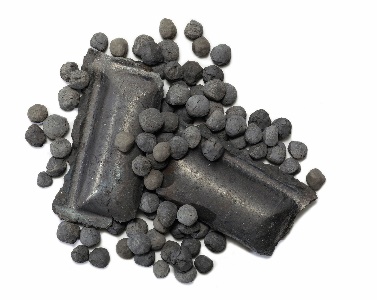
Compiled from articles previously published in Direct From Midrex and information prepared by HBI Association by Frank Griscom, Griscom Consulting, Charlotte, NC, and edited by Dr. Sara Hornby, Global Strategic Solutions, Charlotte, NC, and Dr. Vincent Chevrier, General Manager-Technical Sales and Marketing, Midrex Technologies, Inc.
INTRODUCTION
Quality of ferrous scrap is primarily measured by melting yield, density, physical size, and chemistry. While the first three features have significant economic and operational implications, chemistry – and particularly, residual element/ material content – has the greatest effect on final steel quality.
With each improvement in steel production technology and know-how, the supply of high quality revert scrap declines. Although the number of automobiles scrapped is much greater today, the use of plastics, alloys, and other contaminating materials is increasing. Likewise, supplies of industrial scrap, such as clippings, trimming, and turnings are declining as metalworking becomes ever more sophisticated.
Scrap quality is never guaranteed and can vary from region-to-region, type-to-type, and even lot-to-lot. But DRI brings out the best in a scrap charge because it offsets many of the shortcomings of scrap, as shown in the Figure 1 comparison.
The value of direct reduced iron (DRI) as a diluent to scrap cannot be overstated nor should it be overlooked or discounted when compared to some of its other attributes: melt consistency, predictable chemistry and heat & mass balance, nitrogen control, productivity, and power benefits when DRI is continuously hot charged at much higher temperatures than scrap. The diluent effect of DRI is a feature that can benefit all electric arc furnace (EAF) operators regardless of the steel grade they produce.
FIGURE 1. Comparison of scrap and DRI
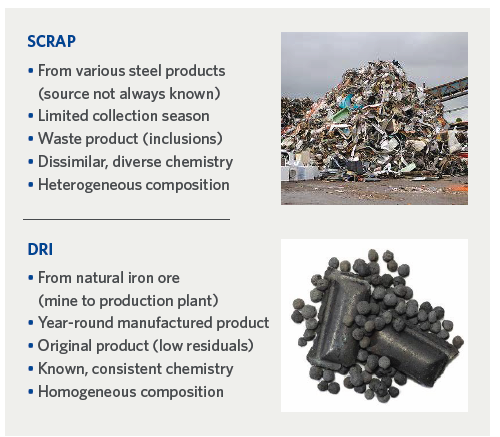
CARBON STEEL QUALITY
EAF steelmaking has come a long way in a relatively short time, and the driving force has been “higher quality.” There have been major strides in equipment, techniques, and practices since the EAF made its debut as a way to make small quantities of basic steel grades from obsolete, discarded steel products. Today, major steel companies throughout the world are using EAFs to produce everything from high-strength rebars to steel sheets for automobile body panels and electrical steels.
Of the four steel types or groups – carbon, alloy, stainless, and tool – carbon steel accounts for 90% of production. Carbon steels only contain trace amounts of elements besides carbon and iron. The key factor distinguishing low/mild, medium, and high carbon steel is the percentage content of carbon in the steel: mild (0.4-0.3%), medium (0.3-0.6%), and high (0.6-1.5%).
Low (Mild) Carbon Steel
Due to its low strength, softness, and ductility, it is easily shaped and machined. Low carbon steel, often called mild steel, includes most carbon steel, as well as high-quality carbon steel used for engineering structural parts. Low carbon steel is generally not heat treated before use and is generally rolled into angle steel, channel steel, I-beam, steel pipe, steel strip or steel plate for making various building components, containers, boxes, furnace bodies, and agricultural machinery. High-quality low carbon steel is rolled into thin plate to make deep-drawn products, such as automobile cabs and engine covers. It also can be rolled into bars for the production of mechanical parts with low strength requirements.
Medium Carbon Steel
Medium carbon steel is a balanced combination of strength, ductility, and toughness. It includes most of high-quality carbon steel and a portion of plain carbon steel. It has good thermal processing and cutting performance but its welding performance is poor, so preheating is required before welding. Cold-rolled or cold-drawn material can be used with or without heat treatment. Medium carbon steel is mainly used to manufacture high-strength moving parts, such as air compressors; pump pistons; steam turbine impellers; heavy machinery shafts, worms, gears, etc.; surface wear parts; crankshafts; machine tool spindles and rollers; bench tools; and more.
High Carbon Steel
High carbon steel has high strength and hardness, is wear resistant but has lower ductility, which renders it harder to shape. It can be quenched and tempered; however, cracks are easily generated during water quenching due to its high carbon content so two-liquid quenching is often used, as well as oil-hardening for small-section parts. High carbon steel is mainly used in the manufacture of springs, wear parts, and high-hardness tools.
FIGURE 2. Typical residual limits in carbon steel products
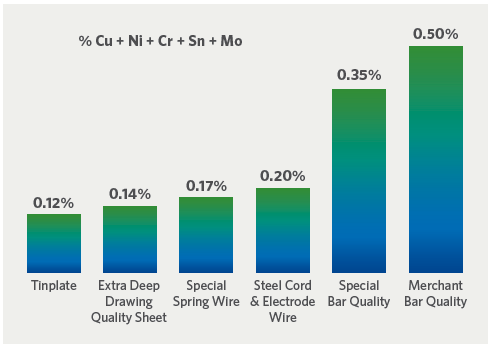
THOSE TROUBLESOME RESIDUAL ELEMENTS
While melting yield, charge density, and the physical size of scrap have significant economic and practical implications for EAF steelmakers, chemistry – and particularly residual element content – has the greatest impact (see Figure 2). The control of these elements is probably the most persistent challenge to EAF steelmakers (Note: The term “residual elements” in this article refers to those elements not intentionally added to the steel that are difficult, if not impossible, to remove from the bath during the steelmaking process. For this reason, they are also called “tramp elements”).
Table 1 lists the various residual elements and materials commonly found in and on scrap, how they are removed in steelmaking (if possible), and how they affect steel products. Those not preferentially oxidized versus Fe tend to stay in the steel.
The following briefly describes the effects of some of these elements on EAF operations (also, see Table 2):
- Cu, Ni, Mo, Co, Sn, As, and Sb – tend to harden the steel and make it more difficult to roll.
- Si, P, Cr, and Al – lower the basicity of the slag and make it more difficult to remove sulfur and phosphorus in the heat.
- Zn and Pb – volatilize and affect refractories, fume collection equipment, and effluent water.
- S – exerts negative influence on steel properties and is difficult to remove, which results in lower productivity.
- Oil, grease, paint, plastic, rubber, and organic fibers – reduce liquid steel yield, produce heavy fumes, introduce sulfur into the melt, and affect melt chemistry control.
- Dirt, sand, glass, clay, and concrete – contribute to larger slag volume, which results in lower liquid steel yield.
Light scrap, used as a “cushion” for larger, heavier scrap layers in the EAF, can be detrimental also. It oxidizes rapidly resulting in increased furnace lining wear, poor melt chemistry control, lower liquid steel yield, and decreased productivity.
Because most of “the big five” residual elements (copper, nickel, chromium, tin, and molybdenum) are not oxidized during the steelmaking process, they tend to concentrate and harden the steel. Equally disturbing is variability in the chemistry of the liquid steel from melt-to-melt, especially the level of residual elements. These can cause hot shortness (embrittlement of steel during hot working) and surface hot shortness (formation and concentration of low melting temperature compounds along grain boundaries), which affects surface quality.
Thus far, no one has found an economically feasible way to remove the most troublesome residual elements (copper, tin, nickel, molybdenum, arsenic, and cobalt) from liquid steel. Vacuum treatment can be used to remove some of the more volatile residual elements, but the removal rate is too slow for most of them.
Chlorine-based reagents have been considered for tin removal, but large iron losses associated with this treatment preclude its practical application. Similarly, calcium can remove some arsenic, antimony, tin, and nickel but the efficiency is far too low to justify the use of this expensive reagent.
Sodium sulfide has been studied for the removal of copper and tin; however, this treatment requires high carbon and low temperature, as opposed to low carbon and high temperature associated with liquid steel.
TABLE 1. Common constituents in/on scrap and their effect on steelmaking
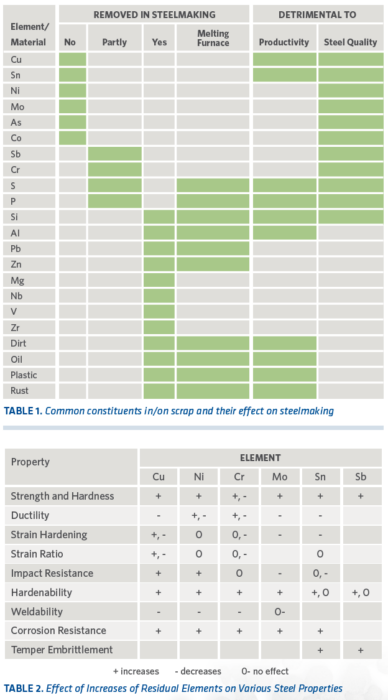
TABLE 2. Effect of Increases of Residual Elements on Various Steel Properties
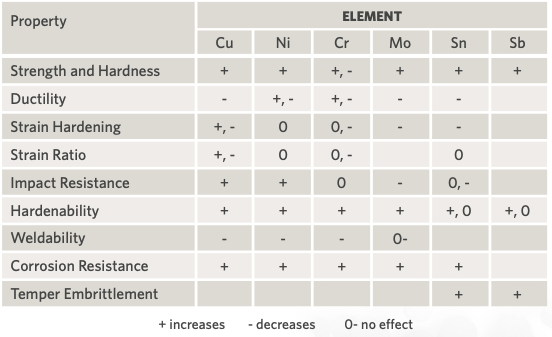
UNTIL THE DAY COMES WHEN EACH PIECE OF SCRAP IS INDIVIDUALLY ANALYZED AND SORTED, THE DIFFICULTY IN IDENTIFYING TRAMP ELEMENTS IN OBSOLETE SCRAP WILL CONTINUE TO FRUSTRATE USERS AND SELLERS ALIKE.
DRI TO THE RESCUE
EAF steelmakers are well aware of the increasing contamination of scrap. The immediate solution sounds simple: improve scrap segregation to separate “clean” scrap from the undesirable materials. While this solution is logical and seems practical, the realities of scrap collection, processing, and brokering prove to the contrary. And it does not take care of the in-situ tramp elements. The scrap industry is highly competitive and cost-conscious. While steelmakers want better scrap segregation, they still expect the lowest price, which does not support investment in better equipment and facilities and the manpower to operate them. This is the primary reason a growing number of steel producers are investing in scrap collection and processing.
DRI has none of the vagaries that surround scrap collection and processing because it is manufactured from natural iron ore, having known chemical content, without melting. As a result, the DRI contains only iron, gangue (silica and alumina), carbon (typically 1-2%), and a small amount of unreduced iron oxide. The gangue constituents are removed in the EAF slag and the carbon reacts exothermically with the unreduced iron oxide in the DRI, thus generating carbon monoxide, which is not only useful in foaming the EAF slag but also helps purge nitrogen and hydrogen from the metal bath. Any excess carbon in the DRI post-reduction reacts with oxygen or oxides in the bath augmenting the carbon effect.
The advantage of DRI for controlling residual elements is evident when comparing the residual levels in DRI (traces to < 0.1%) with various grades of scrap (0.1-0.6%). DRI is even “cleaner” than blast furnace pig iron, which is contaminated by coke, sulfur, and fluxes.
The impact of DRI on final steel chemistry can be seen in a comparison of copper levels in steel produced from 100% #1 HMS and a charge mix of 30% DRI-70% #1 HMS (Figure 3). The copper range in the 100% #1 HMS steel is 0.25-0.45%, while the copper range in the 30% DRI-70% #1 HMS is slightly more than 0.20-0.30%.
It should be noted that the variability of the copper level as well as the amount of copper is reduced, which is equally important in determining the quality and value of the final steel product.
In addition to the control of residual elements, the use of DRI in the EAF limits the amount of sulfur, phosphorus, and nitrogen in the liquid steel and provides for more consistent product quality. Benefits include: lower yield strength (improved malleability, more elasticity) due to less residuals and nitrogen content, improved surface quality from less free oxygen in the bath, greater predictability of mechanical properties after heat treating, and more resistance to strain aging.
FIGURE 3. Influence of DRI on copper variability
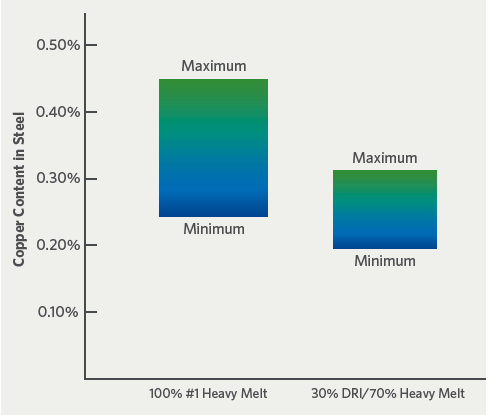
CONCLUSION
When DRI made its first appearance in modern steelmaking, it was somewhat jokingly called “sponge iron” due to its porous nature. Early on, it was used primarily in scrap-deficient regions and became known as a scrap substitute. When DRI started to turn heads in more established steel producing economies, such as the US, it was at first considered a scrap alternative and seen primarily as a means to affect the price of steel scrap. Today, DRI is rightfully known as a scrap supplement for EAF operations and as a burden enrichment for blast furnace hot metal production. For the future, it will be regarded as the preferred source of ore-based iron units for low carbon emissions, hydrogen-based steelmaking, according to the International Energy Agency (IEA) Iron & Steel Technology Roadmap.
If the steel industry ever needed a superpower, it’s now. Regardless of what it is called, DRI will continue to grow in importance as steel producers strive to meet stricter CO2 emission standards while sustaining profitable operations.
For further insights into hydrogen-based DRI and its role in green steelmaking, see the following:
- “Impact of Hydrogen DRI on EAF Steelmaking,” by Dr. Sara Hornby, Global Strategic Solutions, Charlotte, N.C. USA, and Prof. Geoff Brooks, Swinburne University of Technology, Melbourne, Victoria, Australia; 2Q2021 DFM.
- “Future Processing Options for Hydrogen DRI,” by Dr. Sara Hornby, Global Strategic Solutions, Charlotte, N.C. USA, and Prof. Geoff Brooks, Swinburne University of Technology, Melbourne, Victoria, Australia; 4Q2024 DFM.
- IEA paper referencing hydrogen DRI associated with CCUS in the future of steelmaking – www.iea.org/energy-system/industry/steel.
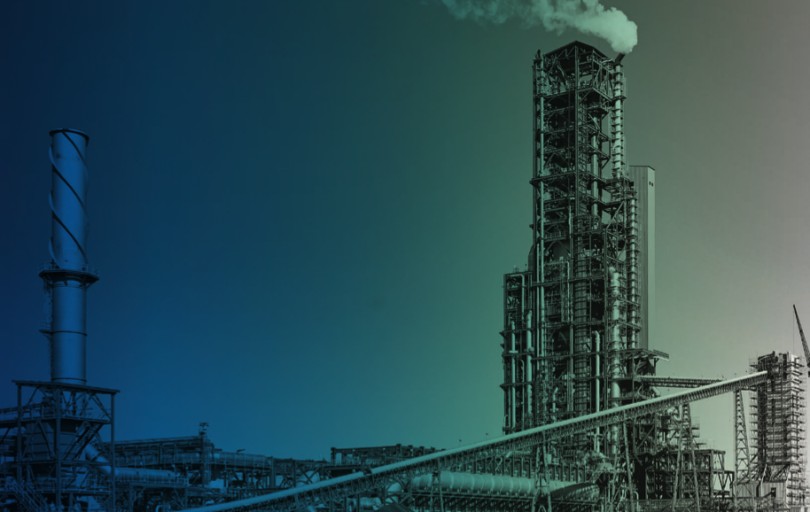