Hydrogen in Iron and Steelmaking: Ore-Based Metallics & Carbon-Neutral Steel
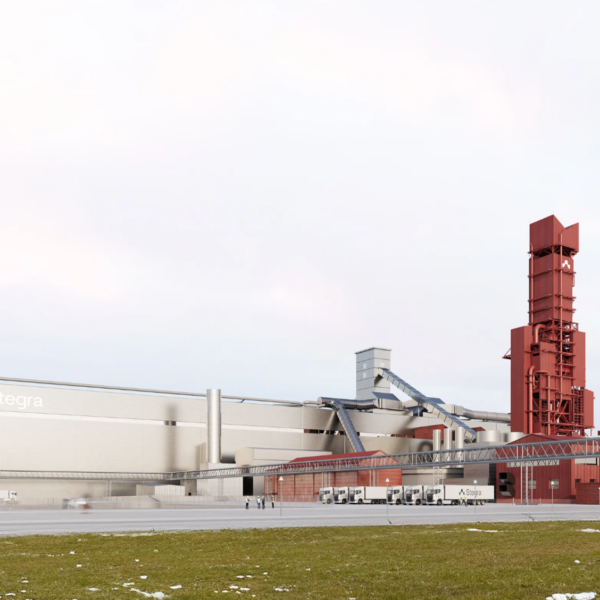
This article is based on excerpts from IIMA White Paper 7: “Hydrogen in Iron & Steelmaking” by Neil Bristow, H&W Worldwide Consulting, and Chris Barrington, IIMA Chief Adviser, April 2024, reviewed and updated by Christian Boehm, Primetals Technologies Austria GmbH, and Chairman of IIMA Technical Committee.
INTRODUCTION
The global steel industry accounts for between 6-8% of carbon dioxide (CO2) emissions. The majority of this is due to the reduction phase of iron ore in blast furnaces (BFs). While modern ironmaking systems have seen a sizeable reduction in emissions and an increase in energy efficiency in the past 20 years, to reach the targets of net zero emissions by 2050, a non-carbon, fossil-free reductant will be required. This will result in the large-scale use of hydrogen as the key reductant in ironmaking technologies.
This article outlines the different types of hydrogen, explores the costs of producing hydrogen, discusses the use of hydrogen in iron and steelmaking to replace carbon reductants, and touches on future issues and uncertainties surrounding widespread adoption of hydrogen as the primary reductant in producing iron for steelmaking applications.
INTRODUCTION TO HYDROGEN
What is Hydrogen?1
Hydrogen is a colourless, odourless, tasteless, and non-poisonous gas under normal ambient conditions. It exists as a diatomic molecule, meaning each molecule has two hydrogen atoms (H2). Hydrogen is the smallest, lightest, and the most abundant element in the periodic table.
Hydrogen can be stored and consumed as liquid hydrogen or compressed gaseous hydrogen. Liquid hydrogen must be kept at -253oC at 1 bar. Compressed hydrogen must be stored at 200 – 700 bar at ambient temperature. The boiling point of hydrogen at atmospheric pressure is -253oC, which is 20oC above absolute zero and far colder than the boiling point of nitrogen (-196oC) and liquefied natural gas (-162oC). This presents major challenges in adapting existing liquified natural gas infrastructure for liquid hydrogen storage and transportation use, even in the case of hydrogen being transported in the form of methanol or ammonia carriers followed by dissociation and separation.
While hydrogen may dissipate quickly in open, well-ventilated areas, confined spaces with little or no ventilation represent a significant hazard. Combustion may occur in some scenarios depending on the flammable air temperature, gas pressure, and location of a leak. These characteristics will require corresponding electrical equipment certification for application in hazardous areas.
Hydrogen has a wide flammability range compared to other commonly handled fuels and cargoes and a maximum experimental safety gap of 0.29 mm, having an assigned 11C gas group based on the international method of area classification developed by the IEC (International Electrochemical Commission.
Although the heating value of hydrogen is the highest of all potential fuels (120-142 MJ/kg), the energy density per volume is relatively low at standard temperature and pressure. This can be increased by storing hydrogen as a compressed gas or in liquified form, but even in these forms the energy density is significantly below that of other hydrocarbons and alternate fuels; e.g., ammonia, methanol, and liquefied natural gas (LNG).
THE HYDROGEN RAINBOW
Hydrogen is given different “colours” to differentiate the various production methods (see Table 1).
Although there are many ways to produce hydrogen to reach net zero emissions, green hydrogen will need to be produced in very significant volumes. This will pose major technical and commercial challenges and will require massive government and/or private funding to enable development of the volumes of green hydrogen needed for industry and power generation.
Pink hydrogen is something of a niche product in the current market but has significant longer-term potential to add to the supply of low emission hydrogen. Nuclear energy is used to generate the heat required for high temperature steam electrolysis, without the intermittency of renewable sources of wind and solar power. Of course, nuclear power brings its own challenges: although CO2 emission is not an issue, there are the attendant problems of long-term storage of nuclear waste, safety concerns and public acceptance. These challenges will have to be addressed if pink hydrogen is to fulfil its potential.
White hydrogen is experiencing an increased level of interest and visibility and has been referred to as “the white gold rush.” There were 40 companies exploring for natural hydrogen deposits by the end of 2023, up from 10 in 2020. A key incentive driving this “gold rush” is that natural hydrogen would have a significant cost advantage over hydrogen produced from renewable energy or fossil fuels. Whereas grey hydrogen costs less than US$2/kg on average and green hydrogen currently is three times more expensive, white hydrogen could be extracted and purified at a cost of about US$1/kg. There is currently only one producer, Hydroma, a Canadian company, which operates a well in Mali at an extraction cost of US$0.50/kg. Recognising that it is at an early stage of development, white hydrogen could be a gamechanger for the low emission hydrogen sector, although reserves still have to be quantified and the issues of transportation, distribution, and storage have to be addressed as for all forms of hydrogen.3
TABLE 1. The Hydrogen Rainbow2
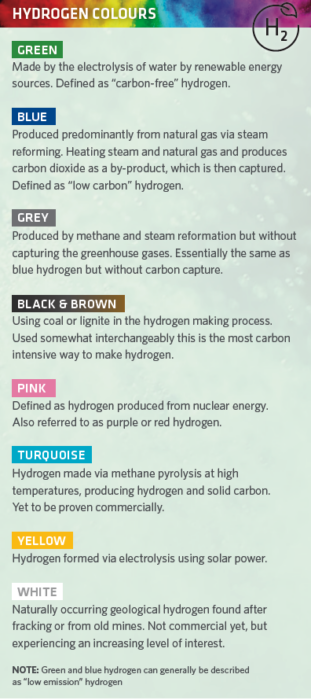
COSTS OF HYDROGEN
The two main routes for achieving net zero emissions by 2050 are likely to be electrolytic production of hydrogen and the addition of carbon capture, utilization, and storage (CCUS) to conventionally produced hydrogen from fossil fuels, green and blue hydrogen respectively. The key will be the production of hydrogen via the electrolysis route using ever larger and lower-cost electrolysers.
Based on existing proposed projects, low emission hydrogen could move from 0.7 Mtpa in 2021 to around 24 Mtpa by 2030. The future of many of these projects depends on improving electrolyser technology and the development of sufficient green electricity to power them. Australia is one of the leaders in the proposed use of renewable electricity-powered hydrogen production, with targets of electrolyser capacity of 50 GW by 2030. This equates to more-or-less the amount of power required to power all homes in Australia. One of the key features here is the continued reduction in the costs of renewable electricity and water, necessary to drive cost-effective hydrogen production.
Larger capacity electrolysers are currently under construction in Europe (32%), Australia (28%), and Latin America (12%).2 Scale is predicted to exceed 260 MW by 2025 and >1 GW by 2030. To reach these targets significant additional funding will be required, which is proving a challenge. Electrolyser capacity is being expanded to meet future demand and planned capacity. If funded, it will be more than sufficient to meet projected demand. This will be extremely important if the global steel industry moves to high hydrogen use towards and beyond 2030.4
Costs of electrolyser capacity will be a function of size and location. To produce green hydrogen an electrolyser will need to be powered by green electricity, which will pose major challenges and difficulties (e.g., renewable power is not continuously available from solar and wind and the limited expansion potential for hydropower) and will need significant expansion of renewable power generation feeding the grid. Estimated production costs vary from around US$4/kg hydrogen to >US$9/kg, depending on location9. The cost of hydrogen is predicted to come down as the efficiency of electrolyser technology improves, from <70% to approximately 85%, and targets of between US$2.3 to <US$4.0 have been forecast.10 Current costs using steam reforming generation of hydrogen are in the order of US$1.00/kg.
Electricity cost is one of the key components to the overall cost of producing hydrogen, with estimates of between 50-55 kWh required per kg of hydrogen, equating to around US$3/kg at a power cost of US$0.06/kWh.9 Typical costs for green electricity are higher than this and vary by location but are in the order of US$0.08-0.12/kWh. Costs in developing countries are higher than in regions with advanced electricity grids and will need to see major electricity grid advances to make hydrogen costs economically viable. More recently, the cost differentials between renewable power and fossil fuels have declined9,10 and further cost reductions are needed to continue this trend, particularly for solar and offshore wind power generation. It is expected that lower hydrogen production costs will enable large scale hydrogen generation facilities to come on stream in the next decade.
The cost of electrolysers is another major consideration. Current full costs are in the range of US$1,400 to US$1,800 per kW. Major reductions in costs of up to 70%2 are predicted by 2030, with a target of around US$400 per kW by 20309 and ~<US$300 per kW by 2050, as economies of scale and technology proceed2. A key uncertainty will be the cost of metals; e.g., platinum and rare earths, which are critical parts of both alkaline and membrane electrolysers.
CCUS coupled to use of fossil fuels could enable hydrogen production of 3 Mtpa by 2030 in Europe, with a similar level in North America. The key here is the successful, timely development of lower cost CCUS options. Although technically CCUS can work, the major issue will be can it become commercially viable, as this will require a continued reduction in costs. A major cost driver for CCUS is the steam requirement of approx. 1 tonne of low-quality steam per tonne CO2 captured. The total potential CCUS project pipeline is as high as 80 Mtpa CO2.
Another issue is the cost of storage of either electricity or hydrogen to buffer intermittent green electricity generation and steady industrial demand, both daily and long term. Storage of either is expensive and not available yet at industrial scale. The cost of CCUS is highly variable and depends on the levels of CO2 in the gas streams. Typical costs for CO2 capture from concentrated gas streams vary from around US$15-20/t CO2 to US$40-120/t CO2 for dilute gas streams. Indicative costs for CO2 capture are shown in Figure 2.14
To reach net zero emissions by 2050, most forecasting groups suggest that this will require the adoption of CCUS. Use of CCUS and/or green hydrogen in the steel industry is the projected route most likely to enable such low or zero emission targets by 2050 in developed regions such as the EU, North America, and north Asia.
HYDROGEN PRODUCTION
Hydrogen is not yet viable at scale. According to the IEA (International Energy Agency), green hydrogen will not be available at an industrial scale until after 2030 – currently less than 0.1% of global dedicated hydrogen production comes from water electrolysis. In the interim, blue hydrogen options are being explored. However, the main challenge will still be in producing hydrogen at scale to meet projected demands, not only from the iron and steel industry but also from the other industry sectors. Under IEA’s Sustainable Development Scenario, global demand for hydrogen will increase to 287 Mtpa by 2050, which represents an increase of over 400% from 2020.30
The demand for hydrogen will increase strongly to 2030 and beyond. However, as yet there is no priority in the demand for hydrogen. It has not been determined which industry will receive the available green hydrogen as-and-when it becomes available. Potentially, this might come down to simple price/affordability criteria. There is a shift nowadays to favor industrial use vs. other sectors (such as transportation) that can better afford hydrogen.
Hydrogen production is nevertheless growing strongly, with numerous projects worldwide to produce the different forms of hydrogen. Production of green hydrogen is predicted to grow very strongly post 2030, as shown in Figure 3, and will become the dominant form of hydrogen by 2050.14 Blue hydrogen also will increase while grey and brown hydrogen produced from fossil fuels will decline post 2030.
FIGURE 2. Costs of CO2 capture by sector (US$ per tonne)14
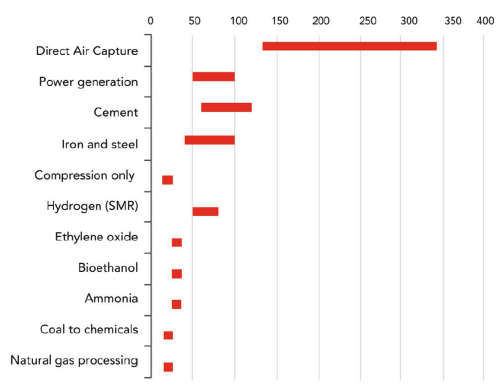
FIGURE 3. Global hydrogen production by colour: 2022 to 2050 (Mtpa)15
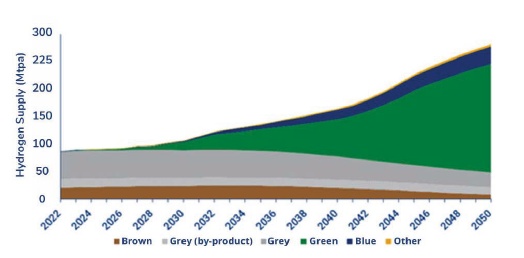
HYDROGEN IN IRON & STEELMAKING
The conventional route currently used in the production of steel is ~72% via the cokemaking/blast furnace/basic oxygen furnace (CO/BF/BOF) route and ~29% via the scrap/DRI/electric arc furnace (EAF) route, worldwide. The blast furnace route emits up to four times more CO2 than the EAF route. The major source of the CO2 via the blast furnace route is the sintering and iron ore reduction/ smelting processes (see Figure 48).
The direct use of hydrogen for iron and steelmaking is for heating purposes and for the reduction of iron ore oxide. Three main application fields for the utilization of hydrogen within the iron and steelmaking exist:
- Hydrogen injection in blast furnaces: here a partial replacement of coke or pulverized coal as PCI and/or the replacement of natural gas or other reductants with hydrogen is possible but limited. As hydrogen reduction is endothermic, it absorbs heat and results in a cooling effect in the blast furnace raceway, which needs to be compensated with additional heat added to the reduction and melting process inside the blast furnace. This reduces carbon emissions but does not eliminate them entirely.
- Hydrogen Plasma Smelting Reduction (HPSR): This is a process that uses hydrogen plasma to reduce iron ore, which is still in experimental stages but has certain potentials.
- Hydrogen-based Direct Reduced Iron (H2-DRI): Instead of using natural gas or coal, hydrogen can serve as a reductant to remove oxygen from iron ore. This process produces water (H2O)instead of CO2, making it more environmentally friendly.
Most major steel companies have published emission reduction targets, with the majority seeking to achieve 25-30% or more by 2030, while aiming for net zero emissions by 2050. As part of these ambitions to decarbonise the steelmaking process, the widespread use of hydrogen has been planned. This will be focused on technology seeking to replace natural gas with hydrogen in direct reduction processes and partially replacing pulverised coal injection (PCI) with hydrogen in the blast furnace. This will be undertaken in staged processes.
For hydrogen to be used in combination with CO in direct reduction shafts, significant planning has been done on moving to increased levels of hydrogen and then to full 100% hydrogen reduction. Where there is the practical option to store CO2 geologically, carbon capture and storage also can be added to the process to reduce the carbon footprint for existing direct reduction plants and/or blast furnaces. Partial use of captured CO2 already occurs in Mexico and Abu Dhabi, for example.17 Most major European steelmakers have plans to add DRI capacity to their steel plants by or soon after 2030.
It is worth noting that HBI could also be seen as a form of energy transport. HBI manufactured in green or low emission hubs, for example in the USA, Middle East, Australia, etc. and shipped to countries with high energy cost and/ or limited potential for renewable energy, would be a much simpler and lower cost solution than transportation of hydrogen as liquid, gas, or ammonia.
FIGURE 4. CO2 emissions during CO/BF/BOF steelmaking by stage (T CO2/T HRC)8
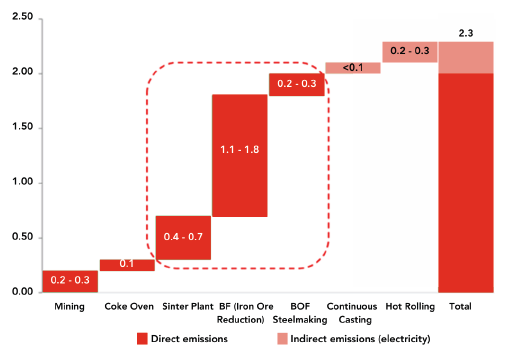
Hydrogen-based Direct Reduction
Flowsheets for 100% hydrogen-based reduction have been developed for both the MIDREX® and ENERGIRON® processes. In addition to the established direct reduction processes, emerging direct reduction technologies, such as Primetals’ Hyfor™ fluidised bed process and the POSCO/Primetals HyREX fluidised bed process combined with a smelter will be hydrogen-based. Metso’s re-emerging Circored™ fluidised bed process is also hydrogen-based.
Plans are also well advanced, especially by integrated steel companies in Europe (including SSAB, thyssenkrupp, Tata Steel Ijmuiden, voestalpine, Salzgitter and Saarstahl) for the transition from blast furnace-based to direct reduction-based iron production with the resultant DRI to be used to complement recycled steel in EAF steelmaking or, via an electric smelting step, as BOF feedstock. Similar plans are also underway in the Asia Pacific region, for example in Australia for replacing the blast furnace at Port Kembla works. There are also hydrogen-based direct reduction plants in China, albeit so far with hydrogen derived from coke oven gas.
H2FUTURE16,24 is a European flagship project for the generation of green hydrogen using electricity from renewable energy sources. Under the coordination of the utility VERBUND, steel manufacturer voestalpine, and proton exchange membrane (PEM) electrolyser manufacturer Siemens Energy, a large-scale 6 MW PEM electrolysis system is in operation at the voestalpine Linz steel plant in Austria.
In the near- to medium-term, most of the new direct reduction plants will be based on natural gas with a progressive shift to low emission hydrogen as it becomes economically available. Both the MIDREX and ENERGIRON processes have flexibility in the proportion of hydrogen in the reducing gas, as well as the ability to include carbon capture technology. However, using hydrogen produced from natural gas for DRI production emits more CO2 than using the natural gas directly.
A front runner in hydrogen-based direct reduction is HYBRIT (Hydrogen Breakthrough Ironmaking Technology) in Sweden, a joint venture of SSAB, LKAB, and Vattenfall.25,26 Having successfully demonstrated the process at a pilot plant in Luleå, the next step is a demonstration plant to be built by LKAB and located at Gällivare, using green pellets from LKAB and green hydrogen based on green electricity from the Swedish grid. SSAB will utilise the green DRI to produce green steel at its Oxelosund works and eventually at its Luleå works, which will be converted to EAF steelmaking.
In Boden, Sweden, Stegra (formerly H2 Green Steel) is advancing toward a 2026 start-up of the world’s first commercial-scale green steel mill powered by renewable energy and based on 100% hydrogen DRI. The state-of-the-art steel mill will have an initial production capacity of 2.5 mtpy fed by a MIDREX H2™ Plant supplied by Midrex and Paul Wurth, with a production capacity of 2.1 mtpy of hot DRI (HDRI) and hot briquetted iron (HBI). SMS group will provide the rest of the steel mill for the production of a broad product mix including advanced high strength steel and automotive steel grades.
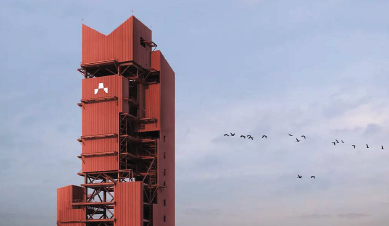
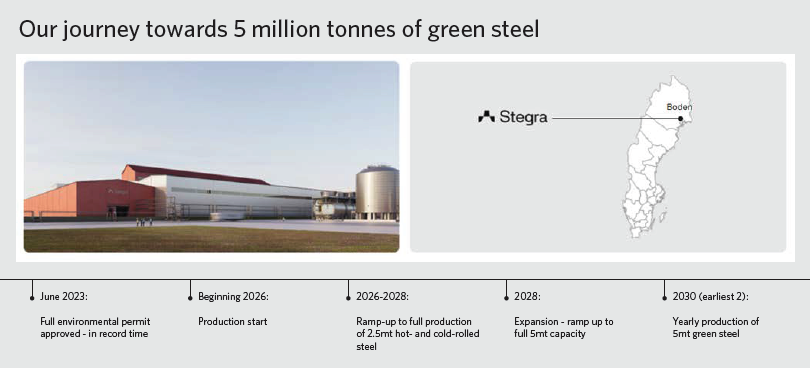
Stegra is pursuing a 5-step development plan for its lighthouse project, with the goal of producing 5 mtpy of “green” steel:
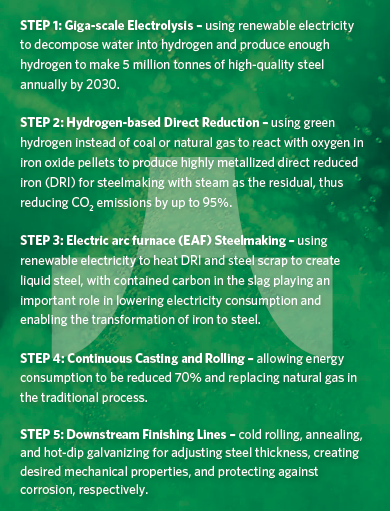
FUTURE ISSUES & UNCERTAINTIES
There are issues and challenges with respect to adoption and use of hydrogen as a carbon replacement in the steel industry. These include:
- Rate of production of green hydrogen: there are numerous projects in the pipeline to produce green hydrogen, but these are wholly insufficient to meet the requirements, commitments, and targets of European steel companies. Tracking the development of such projects will provide a good indication of the feasibility and timeline for the steel companies to meet their stated targets. A key requirement to monitor will be the development of large-scale green power facilities and electrolysers capable of producing large volumes of green hydrogen at commercially viable costs.
- Cost reduction of hydrogen production: aggressive hydrogen cost reduction targets are forecast to 2030. The progress and realisation of these targets will provide good indications of the economic feasibility of reaching net zero emission by 2050.
-
Technical achievement of successful hydrogen use in steelmaking and DRI production: monitoring of the progress of large-scale hydrogen injection into large blast furnaces and the construction of hydrogen-based DRI facilities, for example, the HYBRIT demonstration plant and the Stegra industrial-scale plant due to start in 2026, will be a good guide as to the likelihood of European steel companies reaching their 2030 targets for emission reduction.
-
Development of ranking industries for hydrogen adoption: no such list is currently available. The assessment of industries for available hydrogen when available will allow steel companies to assess their place in the queue and plan accordingly.
-
Evolution of public opinion: current public opinion is strongly in favour of net zero emissions by 2050. However, the economic viability of achieving this target is being increasingly questioned. Many developing countries will not be able to do so. India and China are targeting 2060 and 2070, respectively, and countries in Africa with growing populations do not have targets. In some European countries there already have been some policy-driven slowdowns in the rate of progress towards achievement of key milestones along the pathway to net zero, even as they maintain their 2050 net zero emission goals. Monitoring progress in achievement of intermediate targets; e.g., in 2030, and any changes in public sentiment will assist in determining the rate of adoption of hydrogen use in the steel industry.
Use of hydrogen in shaft furnace-based direct reduction processes will require some technical and operational changes including:
-
Energetics and cooling effect: direct reduction based on hydrogen is different to that based on natural gas as the thermodynamics result in an endothermic reaction delivering a cooling effect inside the reduction shaft. For the case of hydrogen use, some adjustments of temperature and/or gas flow can overcome the cooling effect.
-
Condensation of water: hydrogen reduction forms water. However, this is more of a problem for the blast furnace. Concerning direct reduction plants, if not properly designed and operated, there is the potential for water condensation in the upper regions of the reactor.
A further issue is that a solely hydrogen-based direct reduction plant will produce DRI without carbon, an issue addressed in IIMA White Paper #219 and the article by Dr. Sara Hornby and Professor Geoff Brooks published in 4Q2024 Direct From Midrex, titled “Future Processing Options For Hydrogen DRI.”
References:
(numbers as listed in IIMA White Paper)
1. Volumetric energy density of alternative marine fuels | Marine Service Noord (marine-service-noord.com)
2. Global Hydrogen Review IEA 2022
3. Rystad Energy – The white gold rush and the pursuit of natural hydrogen March 13th 2024
4. Richura Singh, Alisdair Bowles, SPG Global, Global hydrogen demand seen at 614 million mt/year by 2050
8. Steve Randall, Hydrogen Steelmaking Webinar, 7th December 2022
9. “DOE Technical Targets for Hydrogen Production from Electrolysis” energy.gov. US Department of Energy. Retrieved 22 April 2018 and https://www.hydrogen.energy.gov/docs/hydrogenprogramlibraries/pdfs/20004-cost-electrolytic-hydrogen-production.pdf?Status=Master
10. Hydrogen is a trillion-dollar bet on the future, David Fickling, Bloomberg December 2020
14. Is carbon capture too expensive – Adam Baylin-Stern, Niels Berghout, IEA Commentary — 17 February 2021
15. Decoding the Hydrogen rainbow, Wood Mackenzie report, 2023
16. H2FUTURE PROJECT – Startseite
17. Microsoft Word – paper Achieving Carbon Free Emissions via the Energiron DR Process.doc
19. IIMA white papers 1-4
24. voestalpine Supervisory Board approves EUR 1.5 billion for further decarbonization – voestalpine
25. HYBRIT Demonstration – Hybrit (hybritdevelopment.se)
30. IEA: Energy technology Perspectives 2020 https://www.iea.org/data-and-statistics/charts/global-hydrogen-demand-by-sector-in-the-sustainable-development-scenario-2019-2070
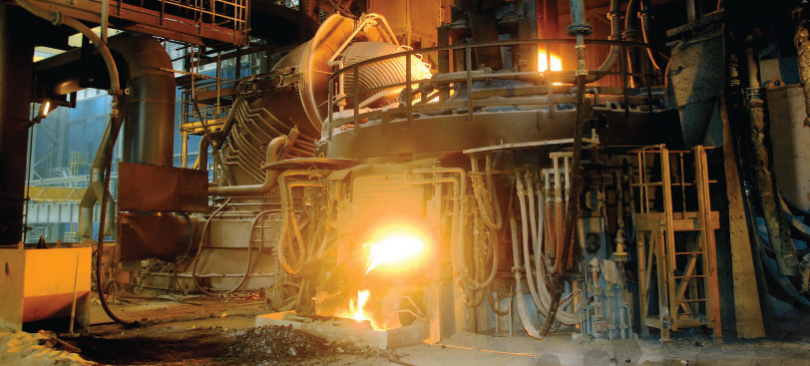