TOSYALI ALGERIE – JEWEL OF THE ALGERIAN STEEL INDUSTRY
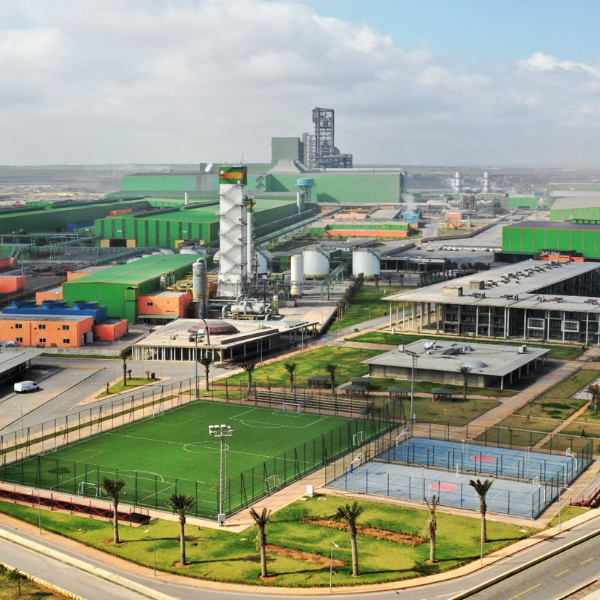
INTRODUCTION
Tosyali Iron Steel Industry Algerie A.Ş. (Tosyali Algerie) is one of 10 key associate companies of Tosyali Holding Inc., primarily engaged in steel production and related industries. Tosyali entered the steel business in 1952 in Iskenderun, Turkey, as a manufacturer of hand-worked stovepipes and boiler buckets. Today, the Tosyali Group is Turkey’s leading global steel manufacturer with 25 manufacturing sites including associates and joint ventures on three different continents operating under the umbrella of Tosyali. Tosyali produces 7000+ steel products broadly classified in nine categories:
- Hot Rolled Steel
- Cold Rolled Flat Steel
- Billets
- Spiral Welded Pipes
- ERW Pipe and ERW Hollow section group
- Low Carbon Steel
- Alloyed and Non-Alloyed Steel
- Wire Rod and Rebar
- Rolled Profile and Angles
Tosyali is the most rapidly growing industrial company in Turkey, with annual manufacturing activity of more than 6 million tons (Mt) while employing 10,000+ of various disciplines. Outside of Turkey, Tosyali is developing a 6 million tons/year (Mt/y) iron ore mining and beneficiation facility in Angola and will establish a 0.5 Mt/y rolling mill in Senegal in addition to the Phase 4 expansion of its integrated direct reduced iron-electric arc furnace (DRI-EAF) steel complex in Algeria, Tosyali Algerie.
DEVELOPMENT OF TOSYALI ALGERIE
Tosyali’s presence in Algeria has reduced the nation’s importation demand, which produces remarkable currency savings.
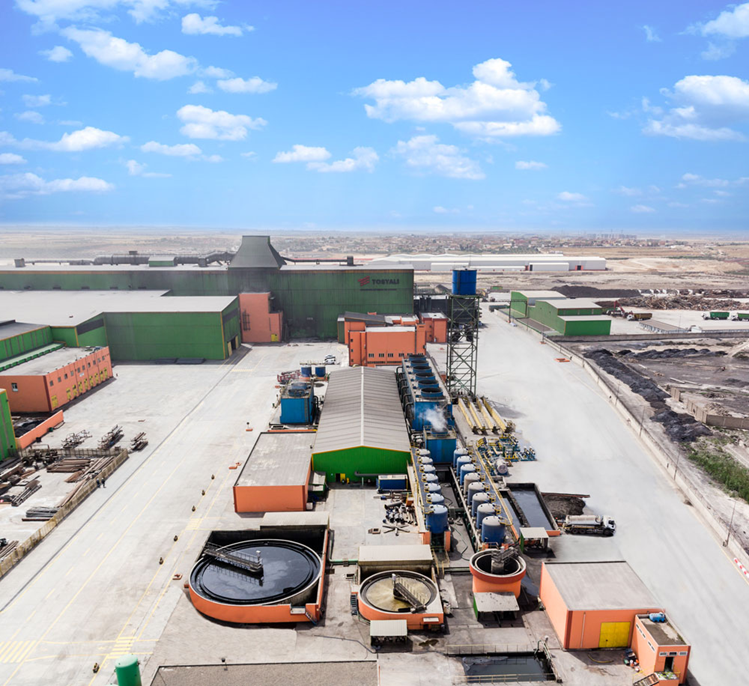
TOSYALI ALGERIE PHASE 1 & 2
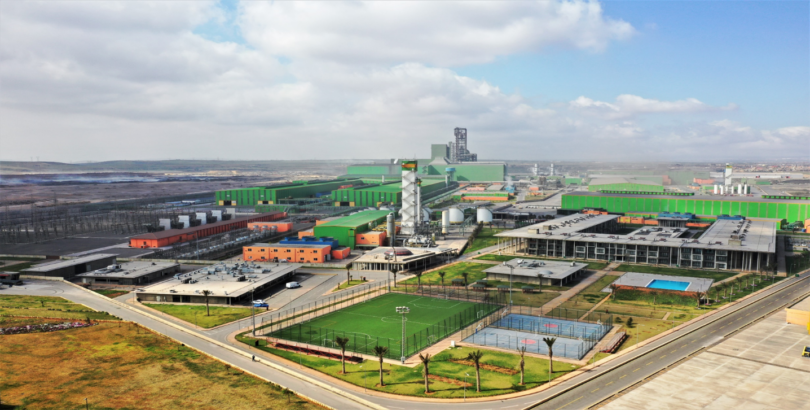
TOSYALI ALGERIE PHASE 3
Tosyali Algerie’s production covers 70% of Algeria’s building materials needs, which are essential for economic development. Ferrous waste (i.e., scrap) from all over Algeria is used as raw material for steel production, and Tosyali Algerie has provided over 4,000 direct jobs and thousands of indirect jobs including high value-added positions and interesting career opportunities for graduates of technical universities in the region.
Tosyali Holding initiated its Algerian operations in 2013 through affiliate company Tosyali Iron Steel Industry Algerie A.Ş. (Tosyali Algerie). The Tosyali Algerie iron and steel complex is located in the industrial zone of Bethioua, 40 km east of Oran. The complex covers 4 million square meters and has easy access to the Mediterranean Sea. Phase 1 included a 1.5 Mt/y EAF steel meltshop and a 1.2 Mt/y rolling mill.
The initial production capacity of reinforcing bar (rebar) was 1.2 million tons and represented 28% of demand at this time. Like reinforcing bars, wire rods are in high demand and a vital product for development.
Phase 2, which was completed in 2015, added a 0.5 Mt/y wire rod mill, which met 60% of the total needs of Algeria at that time. Wire rods are used for the manufacture of dozens of products such as wire mesh, wire, nails, and screws.
The third phase of development started in 2018 aimed to complete the integration of iron ore into the finished product process. In this phase, Tosyali Algerie set up a 4 Mt/y iron ore beneficiation plant and 4 Mt/y pellet production unit to transforms iron ore fines into iron oxide pellets to feed the world’s largest capacity direct reduction module. The combination of pelletizing plant and direct reduction module allows for greater flexibility in sourcing iron-bearing materials and relieves the need for importing costly scrap to feed the steelmaking furnaces. Third phase was successfully completed in 2018 and all production units were put in operation since then.
The DRI plant produces a combination of hot DRI (HDRI) and cold DRI (CDRI). HDRI is directly fed via a hot transport conveyor to the adjacent 2.4 Mt/y EAF melt shop, providing greater EAF productivity and energy savings. Tosyali’s MIDREX® DR Plant has achieved world record DRI production for the year 2020, 2021, and 2022 for a single operating module.
Phase 4 of the Tosyali Algerie steel complex, a DRI-EAF integrated flat steel production facility, began in 2022. In July 2021, Tosyali Holding awarded Midrex and its partner Paul Wurth a contract to build a second DRI plant at the Tosyali Algerie steelworks. The new DRI plant will produce 2.5 million tons of HDRI and CDRI with the capability to operate with increased percentages of hydrogen in the future. HDRI will be fed via a hot transport conveyor to the new 2.4 Mt/y EAF melt shop, providing greater EAF productivity and energy savings. During melt shop outages, the MIDREX Plant can continue producing CDRI up to full capacity.
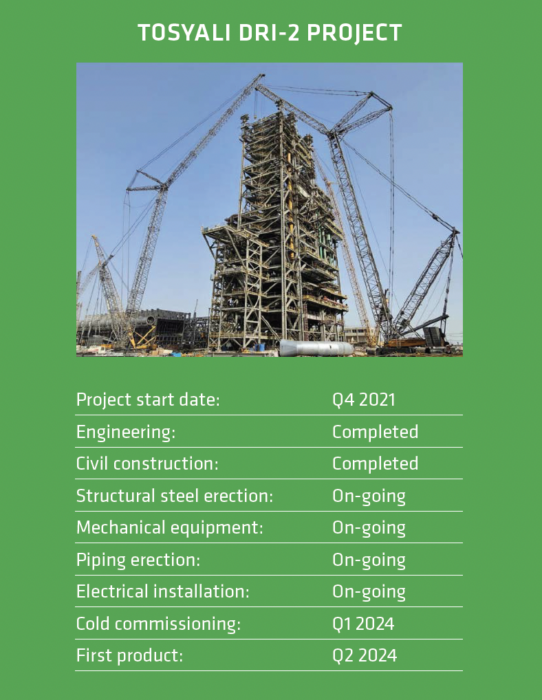
The project will be carried out in two phases with each phase consisting of the following units:
- 4.0 MTPA iron ore beneficiation plant
- 4.0 MTPA iron ore pelletization plant
- 2.5 MTPA direct reduction plant
- 2.2 MTPA steelmaking plant
- 2 MTPA hot strip mill
- 0.8 MTPA cold strip mill
- 0.4 MTPA galvanizing mill
- 0.2 MTPA color-coated coil mill
The hot strip mill along with all upstream units will be put into operation in 2024, while the cold rolling mill and galvanizing will come into operation in 2025.
When the fourth development phase is completed in 2024-25, Tosyali Algerie will join the ranks of flat products producers. The emergence of DRI as a high-quality source of iron and a diluent for the impurities in steel scrap has opened this high-end market to EAF-based steel mills.
Discussions have started with Midrex for the DRI-3 project, which will utilize the MIDREX Flex™ concept for hydrogen transition.
PRODUCTION UNITS
Beneficiation Unit: 4 million tons annual processing capacity
Sinter feed available in the world market is processed through highly flexible circuits of the wet beneficiation method. The process comprises of grinding, magnetic separation, thickening, and filtration to produce 4 million tons of enriched iron ore concentrate containing high ferrous content and low gangue. In the beneficiation process, the size of the iron ore concentrate is controlled by maintaining necessary parameters in primary and secondary grinding mills. Suitable moisture required for the pelletization process is controlled by adopting advanced vertical press filter.
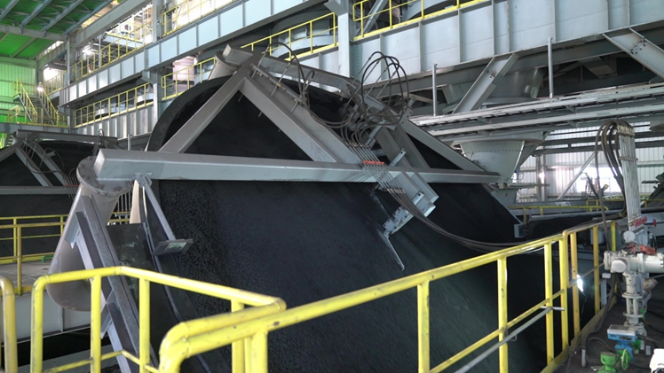
Pelletizing Unit: 4 million tons annual production capacity
The iron ore must be pelletized to 8-18 mm pellets to feed the direct reduction unit. Pellet manufacturing combines chemical, thermal, and mechanical processes to provide the required homogeneous composition of the pellets. The granulation is done in a humid environment in disks to ensure the cohesion of the material. The porosity of the pellets promotes chemical reactions in the direct reduction unit. Once the ore is compacted, the pellets are cooked through burners to enhance their cohesion and eliminate unwanted elements. The iron ore is now ready for direct reduction.
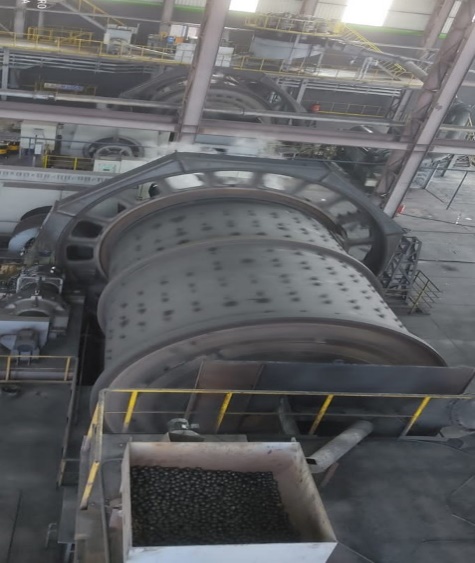
Direct Reduction Unit: 2.5 million tons hot and cold DRI annual production capacity
Direct reduction is a set of chemical reactions using reformed natural gas (mainly hydrogen and carbon monoxide) to transform iron ore into ferritic iron without reaching the melting temperature. The principle is to expose the iron ore to the reducing action of the gas at high temperature (about 1,000° C) to reduce it (remove oxygen).
Our partners for the realization of the direct reduction unit are Midrex Technologies, Inc. and Paul Wurth, world leaders in direct reduction technology. The processing capacity of our facility is more than 300 tons per hour thanks to a continuous production system. This unit offers us a significant advantage in terms of production flexibility and greatly reduces our dependence on purchased ferrous waste (i.e., scrap).

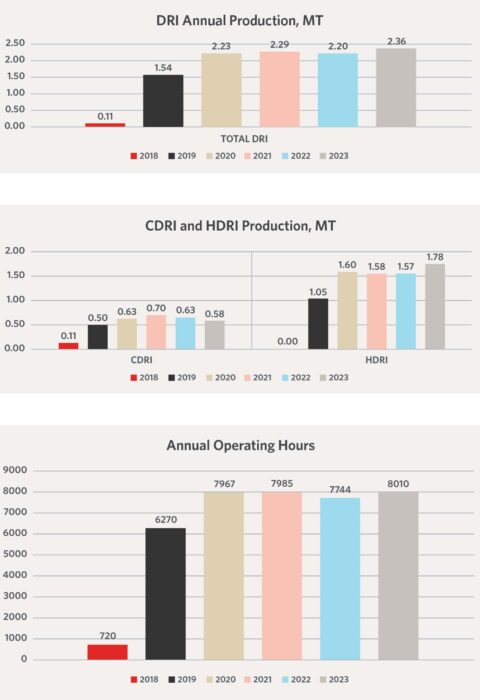
Note: Figures for 2023 in all three graphs are estimates.
VISION, MISSION, VALUES
Tosyali Iron Steel Industry Algerie A.Ş. has the same perspective and objectives as Algeria, to promote the country’s mineral wealth, participate in the development of the high value-added steel industry, create jobs around this sector, strengthen the skills of human resources, eliminate dependence on imports, and move towards export.
It is our basic social responsibility to use the world’s resources efficiently, not to be insensitive to social problems, to contribute to the development of the human resources of our country, and to fulfill our duty towards the institutions, organizations and nongovernmental organizations that make efforts in this direction.
The commitment to sustainable societal and cultural projects reflects the human dimension of our company, the enhancement of skills and natural resources while respecting the environment and the performance of our industry. They serve as resolute steps towards our current and future success.
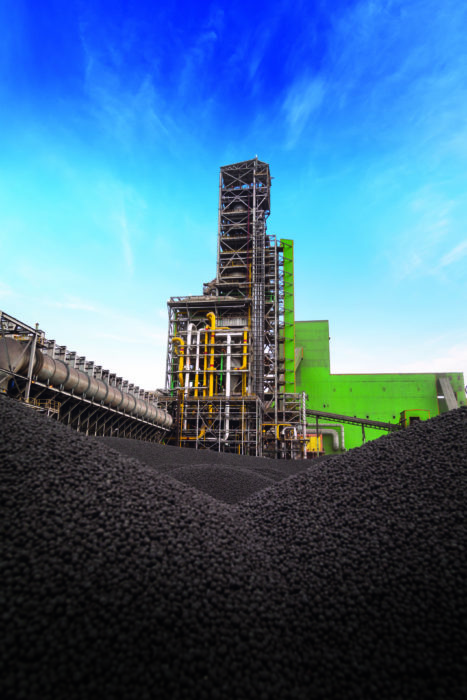